國航工程天津維修基地精益管理項目初見成效
圖:圖為國航天津維修基地定檢施工現(xiàn)場。攝影:王川虎
民航資源網(wǎng)2011年5月26日消息:中國國際航空股份有限公司(Air China Limited,簡稱“國航”)工程技術(shù)分公司天津維修基地把精益理念運用到改善活動中去,以基本生產(chǎn)單元組為自主改善的切入點,在定檢車間啟動A檢流程優(yōu)化精益管理項目,經(jīng)過深入科學(xué)的調(diào)查研究,經(jīng)歷了定義、分析、現(xiàn)場實測、改善實施等階段,歷時近一年,取得了可喜的初步成果。
2010年6月,在項目定義階段,該車間通過對定檢生產(chǎn)流程分析,定義了KPI,確立了以提高生產(chǎn)效率作為考核項目的關(guān)鍵指標(biāo)。運用C&E矩陣等輔助工具,分析得出了影響定檢生產(chǎn)效率的主要因素在于:現(xiàn)階段工作流程不合理以及流程中存在大量的浪費時間。通過評估,制訂了效率提升20%的預(yù)期目標(biāo)。
在測量階段,項目組從生產(chǎn)現(xiàn)場采集了大量數(shù)據(jù),通過Minitab軟件輔助分析的方法,得到了客觀具體的現(xiàn)狀分析結(jié)果。這些客觀數(shù)據(jù)印證了在定義階段的結(jié)論,并且為后續(xù)的分析與改善工作打下了堅實的基礎(chǔ)。
在分析階段,通過對問題的總結(jié),項目組找到了流程改善的出發(fā)點,并且制定了改善計劃與相應(yīng)的方案:一是從車間內(nèi)部出發(fā),通過對組織結(jié)構(gòu)、現(xiàn)場區(qū)域、生產(chǎn)計劃、工序控制、信息發(fā)布等方面的改善,減少浪費,提高生產(chǎn)效率。二是通過與接口單位(航材、工具間、特種車隊)的協(xié)調(diào)合作,減少流程節(jié)點上外部因素造成的浪費,從而提高生產(chǎn)效率。
改善過程并不是一帆風(fēng)順的。其間項目組遇到了許多困難,尤其是對車間組織架構(gòu)的調(diào)整,使得已經(jīng)習(xí)慣了舊體制生產(chǎn)節(jié)奏的員工們很不適應(yīng)。這也使得改善初期的效率提高并不明顯,甚至是降低。其間,在精益專家的幾次遠程及現(xiàn)場指導(dǎo)下,車間全體員工努力適應(yīng)新的運行模式,使改善之路逐漸上了正軌,生產(chǎn)效率也在穩(wěn)步提高。
現(xiàn)在,通過一系列的改善,項目已經(jīng)達到了預(yù)期目標(biāo),提高了將近20%的生產(chǎn)效率,極大地節(jié)約了工時成本,為企業(yè)帶來了更高效益的同時,也提高了自身的競爭力。同時通過6S管理和精益管理,該車間的工作現(xiàn)場和辦公環(huán)境都有了很大的改善與提高。
據(jù)悉,該車間將把要益改善當(dāng)做一項長期的持續(xù)性改善項目,逐步是改善程序標(biāo)準(zhǔn)化、規(guī)范化、智能化、日?;?,實現(xiàn)車間管理工作從“管”到“理”的根本性轉(zhuǎn)變,使其成為促進生產(chǎn)管理和發(fā)展的強有力的工具。
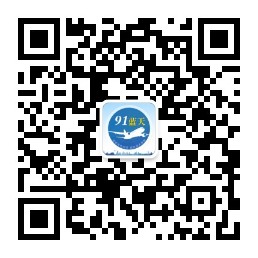